【摘要】 论述了水泵叶片空间曲面的计算和用数控铣床加工的基本方法。并介绍在江苏省江都第一抽水站更新改造工程中成功应用的实例,现场实测结果表明数控加工的叶片能够保证水泵设计性能。
关键词: 水泵 叶片 曲面 数控切削
引言
叶片是叶片泵转换能量的关键部件,原型水泵都是根据小的模型泵按比例放大,准确的叶片形状基本上能保证模型性能在原型上的实现。但是,国内水泵厂生产的各种水泵绝大多数叶片均系铸造成形,叶片表面极少经铣床加工(仅极少数水泵叶片经仿形铣加工,而仿形样板是由手工铲磨而成,难以达到较高的准确性),在不同程度上影响水泵的性能。
江苏省江都第一抽水站是我国最早建成的第一座大型泵站,在运行30年后,于1995年采用国内外较先进的轴流泵水力模型对其进行更新改造。为了保证严格的原型泵性能要求,采用高精度数控铣床加工了叶片标准模,然后用标准模作为样板对原型泵的叶片进行仿形铣加工,确保高精度。
1 叶片空间曲面的数学仿真计算
轴流式叶片表面呈空间扭曲,不仅形状复杂,而且已知断面和数据点很少,模拟难度较大。由于已知断面的数据点是确定叶片形状的唯一依据,故模拟所得的曲面上必须包含全部已知点,即已知点必须全部在此曲面上,这就是曲面数学仿真的原则。
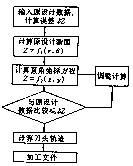
图1 程序框图
在水泵叶片设计时,一般选择5个或6个控制断面,两断面之间的曲面没有较好的参照依据。在制作模型时全凭感觉经铲刮成形,故存在一定的不确定性或随意性。控制断面越多,叶片形状的确定性越好,随意性越小。以前的叶片设计均采用手算、手绘办法,若增加控制断面数,将增加较大的工作量。现在采用计算机辅助设计,可以适当增加一定的控制断面,使叶片表面形状随意性减小。
根据叶片曲面数学仿真的原则,对江都第一抽水站的轴流泵叶片进行曲面仿真计算。对设计数据进行数学处理,通过建立其空间曲面方程Z=f(x,y),对叶片表面进行了全域仿真计算,计算程序框图如图1。仿真叶片曲面与原平联叶片的曲面相比更流畅、平滑、准确,仿真曲面坐标与对应的控制断面坐标列于下表。从图表中数字可知,计算值与设计值极为接近,说明曲面仿真计算结果十分准确。
表 仿真曲面坐标与控制断面坐标比较
x |
Zc |
Z0 |
x |
Zc |
Z0 |
-320 |
105.54 |
105.42 |
-326 |
145.11 |
145.27 |
-275 |
125.57 |
125.54 |
-272 |
165.10 |
165.08 |
-229 |
146.50 |
146.53 |
-217 |
187.12 |
186.93 |
-183 |
168.80 |
168.83 |
-163 |
211.43 |
211.26 |
-137 |
192.94 |
193.00 |
-108 |
238.31 |
238.15 |
-92 |
219.35 |
219.40 |
-54 |
268.03 |
268.00 |
-46 |
248.51 |
248.54 |
0 |
300.87 |
300.91 |
0 |
280.88 |
280.85 |
54 |
337.08 |
337.26 |
46 |
316.91 |
316.87 |
108 |
376.96 |
377.17 |
92 |
357.06 |
357.00 |
163 |
420.75 |
421.01 |
137 |
401.78 |
401.71 |
217 |
468.75 |
468.95 |
183 |
451.55 |
451.46 |
272 |
521.22 |
521.27 |
229 |
506.81 |
506.78 |
326 |
578.43 |
578.16 |
275 |
568.04 |
568.07 |
381 |
640.26 |
639.95 |
320 |
635.67 |
635.80 |
|
|Zc-Z0|max=0.13 mm, 误差的均方差σ=0.065 |
|Zc-Z0|max=0.31 mm,误差的均方差σ<0.162 |
注:Zc、Z0分别为仿真计算值和原始点坐标值。
2 叶片加工坐标计算
叶片曲面形状仿真计算所得尺寸为叶片加工的基本坐标尺寸。在用铣床对叶片进行加工时,由于铣刀的刀头具有一定尺寸,刀头与叶片理论上为点接触而实际上是面接触。因此,准确计算出铣刀加工坐标是保证叶片形状的关键。计算铣刀加工坐标包括:叶片曲面最大曲率的计算、刀头半径选择和加工坐标计算三部分内容。
2.1 铣刀刀头中心点坐标计算 铣刀的行走是根据刀头的中心坐标来确定其路径的,而刀头中心坐标又必须根据仿真计算的基本坐标尺寸和刀头与加工面触点位置来确定。
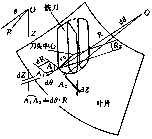
图2 铣刀与曲面接触示意图
铣刀与加工曲面接触如图2所示。铣刀在经过基本坐标点A1到达A2点时,由于A1和A2点均具有一定的斜率,故刀头与之接触不是刀头顶点,而是刀头顶点以外的某点,曲面与刀头在该点相切。为此,在计算刀头中心点坐标时,首先需计算出每一个基本坐标点的切线斜率。斜率可采用解析微分法准确求得,也可用差分法近似求得。这两种方法在坐标点间隔很小时趋于一致。
如图2所示,选取(R,θ,Z)坐标。设刀头沿某一坐标方向,如圆弧方向,行走进刀,从A1到A2,dZ为在Z向的坐标增量,dθ为在θ向的增量,则曲面在A1点的切线斜率为
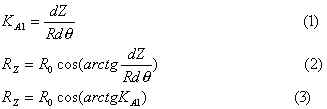
从严格的意义上来讲,需要求出曲面A点的切平面斜率,但由于铣刀刀头曲率半径一般远小于曲面上各点中最小的曲率半径,在铣刀沿某一坐标方向行走进刀时,刀头对其两侧的曲面不会产生过量切削。因此,在这里可以把问题简化到该圆弧所在的柱面内的问题来计算切削点到刀头中心的坐标。
同样如果铣刀沿半径R方向行走进刀,则可把问题简化到该半径所在的轴面内来计算
则
(4)
又
(5)
故
(6)
由式(3)或式(6)可求得计及刀头半径的刀头中心点坐标即加工坐标为
Zm=Z-Rz (7)
2.2 叶片的最小曲率半径和刀头半径选择 为确定合适的刀头半径,需要先求出叶片表面的最小曲率半径,为此,可把曲面分成不同区域先进行比较,在曲率相对较大的区域选择某些典型坐标点进行计算。选择的刀头半径必须小于曲面最小曲率半径。刀头半径越小,可能过切量也越小,但要求行走间距很小,否则,线间连接不平滑。刀头半径越大行间连接越平滑,故在不产生过切加工的情况下,应适当选取较大的铣刀。
2.3 刀头切削轨迹 由于铣刀刀头尺寸影响,加工后的实际轨迹线(即刀头切削轨迹线)与基本坐标点的理论曲线不会完全吻合,实际曲线和理论曲线有一定误差。为掌握这一加工误差,并控制加工误差在一定范围内,必须求出刀头切削加工的轨迹。
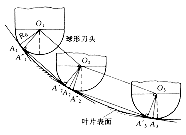
图3 铣刀刀头轨迹计算示意图
如图3所示,当刀头在基本坐标点A1点、A2点和A3点时,均与各点相切,也就是说保证刀头通过A1、A2和A3点,则刀头切削点的轨迹计算如下。
设刀头在不同点时刀头圆心分别为O1、O2和O3点,刀头半径为R0,则刀头球心由O1点向O2点移动时为平移,球心轨迹线O1O2为直线,过O1作 ,使 ⊥A1″A2′,
=R0。很显然, 就是刀头的切削点轨迹,即切削线。因为该线是刀头从O1到O2时刀头公切线(包络线),且 。
同样的道理,当刀头从O2到O3时,刀头切削线为平行于 的 线。
由于刀头到达O2点后,改变了行走路径的方向,切削点由A2′变为A2″点。
这样,由A1到A3各点的刀头切削轨迹为
A1——A1″——A2′——A2——A2″——A3′——A3
在求得铣刀切削轨迹线后,就可以知道曲面的加工误差。一般说来,对于凹面来说,在两基本坐标点之间切削不到位,有一定余量;对凸面来说,则相反,坐标点之间的切削过头,有一定过量。
无论是有切削余量,还是切削过量,其误差大小均取决于坐标点的疏密。因此,对加工精度要求高的,坐标点一定要达到足够数量,点的间隔要小,一般可取点的间隔为1/3~1/5的刀头直径。
关于铣刀加工的坐标计算,目前已有商业软件开发和应用,可在微机工作站上运行,其基本原理相同。
按照上述方法加工叶片的1.75ZLQ-70大泵已在江都一站安装使用,运行两年多来,实测结果表明其流量扬程特性与模型泵性能非常相似,效率指标也基本一致,且运行平稳。实践证明大泵叶片的精确加工是必要的,也是可能的,有明显的效益和良好的应用前景。
刘 超 扬州大学水利学院院长 教授,225009 江苏省扬州市
参考文献
1 沈阳水泵研究所, 中国农业机械化科学研究院 编. 叶片泵设计手册. 北京∶机械工业出 版社, 1983∶298~300 2 Stepanoff A J. 离心泵和轴流泵. 徐行健 译. 北京∶机械工业出版社, 1985∶98~172 3 刘超 等. 江都一站更新改造试验研究. 江苏农学院学报, 1995, 水利专刊∶5~12
THE COMPUTATION AND NUMERICALLY-CONTROLLED MILLING PROCESSING OF PUMP BLADES SURFACE
Liu Chao (Yangzhou University)
Abstract
The methods of computation of space curved surface and numerically-controlled milling processing of an axial flow pump blades are proposed in this paper, which have been applied successfully to the renovation project of Jiangdu No.1 Pumping Station in Jiangsu Province. The results of site measurements give evidence that the numerically-controlled processed pump blades satisfy the requirements of designed characteristics. Key words Pump, Blades, Curved surface, Numerically-controlled milling
收稿日期: 1996-12-19 |