水润滑轴承技术的发展
一.摘要:
早在50多年前,船主们把开式水润滑轴承转换成了油润滑轴承合金艉管轴承。对铁梨木持续供应的过多担心以及唇式密封技术的发展,使此转换得到了发展。艉管轴承提供了一项业已认可的技术,且该技术在艉管轴承的磨损寿命以及保养方面得到了提高。
材料技术的发展已经使轴承在材料方面有了更多的选择。这些材料比铁梨木更能提高磨损寿命。材料技术的发展,伴随着轴承设计的改进,促进了流体动力水润滑轴承的发展。
Thordon轴承—弹性聚合体水润滑轴承技术领域的世界领头羊,一直致力于水润滑艉管轴承的设计。随后,其设计出了流体动力水润滑轴承。该设计以能使支撑元件移动而无须艉轴移动为特色。这些设计已经应用在最新系列的女皇巡洋舰和狄斯尼巡逻艇上面,并且得到了认证。
Thordon公司继续进行水润滑轴承技术的研究,以优化轴承设计和延长水润滑轴承的寿命。新一代水润滑轴承业已成为商业船舶工业中艉管油润滑轴承的可替代品,本论文将强调其发展。
二.绪论:
早在50多年前,船主们把开式水润滑铁梨木轴承转变成油润滑轴承合轴承,密封在艉管中。铁梨木日益明显的短缺以及能更好的估计艉管轴承磨损寿命的需要,加快了此转换。密封技术的发展为获得更大的承载力以及减少轴承磨损提供了一个可控制的润滑环境,并且,此密封技术的发展也促进了这种转换。
从20世纪中叶到20世纪70年代早期,水润滑材料技术的发展使人们对适用于艉管轴承的材料有了更多的选择。尽管,这些新材料比以前的水润滑轴承具有更低的摩擦系数和更长的磨损寿命,但这些轴承仍然在其承载能力以及其磨损寿命的可预测性方面受到限制。
在20世纪80年代早期,轴承的结构得到了斟酌,并且也研发出了基于流体动力学原理的水润滑轴承,研发出的这种结构把水润滑轴承承载能力提高到了与现用的轴承合金轴承相似的水平。
当今,轴承结构的进一步发展使得船主无须高费用地撤去艉轴就可以进行轴承的拆动、检查和重装,使得在轴承的保养方面有更大的适应性,并且减少操作的费用。研究人员继续轴承材料和开式系统的研发工作,以使轴承磨损寿命和操作更可预测。
三.水润滑轴承的发展史:
用水作为润滑剂始于早期的船用推进器。初期的设计试图采用水润滑巴氏合金轴承,导致了灾难性的后果,水润滑巴氏合金轴承磨损率也非常高,轴承也必须连续的更新。当时的设计者很快发现最适宜的轴承材料是一种被称做铁梨木的既硬又纹理好的木材。把铁梨木切成板条,并且把其组装到一个凹型的槽室内。铁梨木作为艉管轴承,其运转相当好。铁梨木轴承,在清水中运转,能有望持续所需的4年之久(满足轮船进出坞的要求)。
铁梨木由于质量很高,因此变的更难获得,艉管密封的改进,使油润滑轴承合金轴承技术得以应用。这些油润滑轴承具有更高的承载能力和可控制的磨损率。该密封式艉管的可控环境使得可进行现场检测和提供更长的时间来检查。因此,密封系统下的油润滑轴承合金轴承成为艉管轴承应用的标准。
四.轴承材料的发展:
新材料的研究始于本世纪50年代,并从石化工业的发展中获得了动力。这些新材料具有更好的载荷承载力、低摩擦系数和好的抗磨损能力而进入轴承市场。那段时期,水润滑轴承最主要还是应用于海军战舰上。在此阶段的发展中,thordon轴承公司开发出了ThordonXL弹性聚合物材料,随之,研发出了SXL和随之而来的Compac流体动力轴承。
五.流体动力轴承的发展
把水作为润滑剂突破了常规思维,水不像公认的润滑剂——石油那样,具有高的粘度和润滑性。然而,水确实具有有限的粘度和密度,因此,能提供流体动力膜,而所必须克服的难关是从orpm到足以产生能够分离轴和轴承的流体动力润滑膜极限点的速度范围。
上等的水润滑轴承的研发将基于材料和设计,该材料要具有好的自滑性,优良的抗摩擦性。该设计将要求有助于流体动力膜的快速产生。Tordon轴承公司坚信尾轴推进器轴承的性能将得到大副的提高,并且,对影响轴承性能的理论进行了研究,发现不管是在油润滑轴承还是在水润滑轴承中,最重要的变量是流体动力膜的建立。该过程可通过典型的“整理过的曲线”来描述。该曲线图标注了摩擦系数和流体动力参数,如图1所示,并且分为三个主要的润滑阶段。
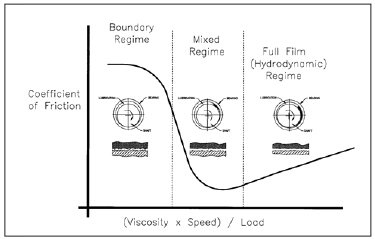
图1 整理后的建设液膜曲线
在第一阶段,轴和轴承直接接触,导致了产生高摩擦量。在这段曲线,轴承的高自润滑性非常有用。随着轴速的提高,我们转到此曲线的第二阶段(混合膜),在此阶段,流体动力膜开始建立,并有效地把轴从轴承的表面提起,这将减少轴与轴承的接触,并很快地减少摩擦。速度继续增长,我们转入第三阶段(流体动压)阶段,在此阶段,;流体动压膜已建立,足以消除所有直接的接触。随着速度的继续增长,摩擦开始增加,这是因为润滑剂的粘度增加了剪切阻抗力。
轴承运转中润滑阶段的转变取决于润滑剂的特性,速度及载荷。曲线的形状和转变点的界面取决于轴体的几何尺寸,相对间隙,轴承材料的自润滑性和轴承表面的光洁度。
高粘度的润滑剂可使轴承在较低的轴速下产生流体动压油膜并且有效的使转变点向左移动。然而,增加粘度也增加了最小的运转摩擦系数,当轴速底于完全的流体动压运转速度时,减小轴承材料的摩擦系数可减小轴承的尺寸,特别是轴承是否有凹槽也影响着曲线。连续的无凹槽的轴承表面比具有凹槽的轴承表面所建立的流体动压膜的厚度更厚(如图2所示)。流体动压计算表明对一个常规凹槽船舶轴承来说,其润滑剂的膜厚是无槽轴承的25%。因此,当采用凹槽设计时,轴和轴承有很大的几率相互接触。
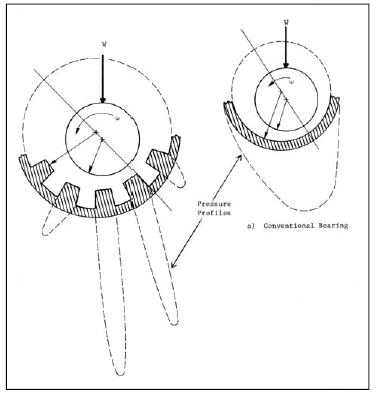
图2 对比建设流体膜压在沟槽和非沟槽海洋的影响.
有史以来,船舶轴用推进器水润滑轴承几乎都是凹槽式的。铁梨木是常用的材料,但由于起尺寸的限制,轴承采用长木板,结合或卡到轴承套内,并且其中间设计有水槽来为了减少对轴承的压力和为建立流体动压膜提供更大的面积,船尾轴承通常以4:1的长径比来设计,而以前的轴承采用2:1。
随着其它材料日益适合替代铁梨木,根据相同的低压值和相结合的水槽它们被设计到相同的轴承套内,然而,这些新材料的全部潜能并未得到利用。
由Thordon轴承公司生产的一种弹性聚合物,使新一代的轴承材料之一,并且在二十世纪七十年代进入了船舶市场。尽管弹性聚合物轴承能够受高压力和表现出非常低的摩擦系数,但也局限于现存设计的惰性,其仅专门以木板条或完全的沟槽,艉管式结构按船尾4:1长径比设计。
由于认识到了本文前面提到的关于船舶推进器尾轴轴承原理的优越性,所以,研究人员开始了一个研究项目。研究人员基于无槽轴承和有槽轴承之间优越性的计算比较,它们选择一个种下平上凹的结构。这平直的下半部分加强了流体动压膜的优化建立。同时,成凹型的上半部分让轴承流过足够的水,以维持流体动压膜和冷却降温。下一个需观测的变量是轴承的长度。由于弹性聚合物轴承与其它材料的轴承相比,具有十分高的承载能力。研究人员曾经做过长径比分别为4:1和2:1的Thordon XL弹性聚合物轴承运转比较试验。在两类轴承上都加以同样的载荷,按长径比4:1设计的轴承其所受的压力为0.24MPa,而长径比为2:1的则为0.48MPa,如图3所示,按长径比2:1设计的轴承摩擦明显的减少。这两类轴承除了在摩擦方面,其它运转特性都相同。在长径比为4:1的轴承的前半部分,由于对水的额外剪切作用,而致使长径比为2:1的轴承摩擦减少。
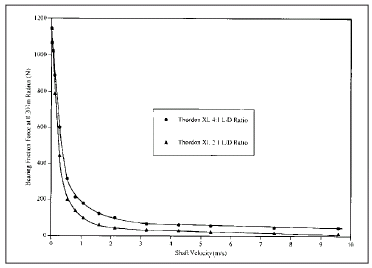
图3 轴承摩擦力与轴的速度
下一步则决定在缩短长径比,从承载区除去凹槽和轴承材料固有的润滑性情况下,轴承总的运转效果就如前面所阐述的那样,当轴承在曲线的第一,第二阶段工作时,采用具有更高的固有润滑性能的轴承材料,能够减少轴承的摩擦。
研究人员现以开发出了一种具有高自润滑性的新型弹性聚合物,也对Thordon XL轴承和平面型橡胶轴承在长径比为4:1和2:1情况下,进行了比较试验,这种新的弹性聚合物在长径比为2:1的结构中被称作Thordon COMPAC系统。这种COMPAC系统试验在图4中展现了曲线怎么移动,阐明了轴承在干摩擦和边界润滑阶段,工作时间的减少以及在液体动压运转时,摩擦水平的降低。静摩擦力矩和工作时的摩擦也都随之减少。轴承也转变成了平滑运转,磨损减少,工作效率提高,现以成功使用的艉管式轴承其工作性能取决于液体动压膜的早期开发研究,该能力将会受到许多因素的影响,包括轴承受到的单位载荷轴承的结构以及轴的线速度。
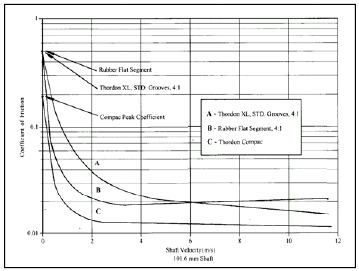
图4
本文共分 1 页 |